In this blog post, we will take a closer look at Order Reduction in SAP EWM. This advanced functionality has been added since SAP EWM version 9.5 version and has been included in S/4HANA versions as well.
This functionality is basically based on Sales order Quantity reduction or cancellation in ERP and how the changes then impact the Warehousing activity – including logistics, execution and delivery.
With a change of Sales order quantity, the below processes are impacted and adjusted.
This functionality is basically based on Sales order Quantity reduction or cancellation in ERP and how the changes then impact the Warehousing activity – including logistics, execution and delivery.
With a change of Sales order quantity, the below processes are impacted and adjusted.
3 business cases will be explained in detail regarding how the change of Sales Order Quantity correspondingly impacts the below:
- When Picking is not started in the Warehouse.
- When Picking Warehouse is created but not Confirmed(DPI=1)
- When Picking and Packing is completed(DPI=9)

Configuring Order Reduction:
● At warehouse process type, the WPT for picking process, activate Order reduction allowed indicator.
● At warehouse process type, the WPT for picking process, activate Order reduction allowed indicator.
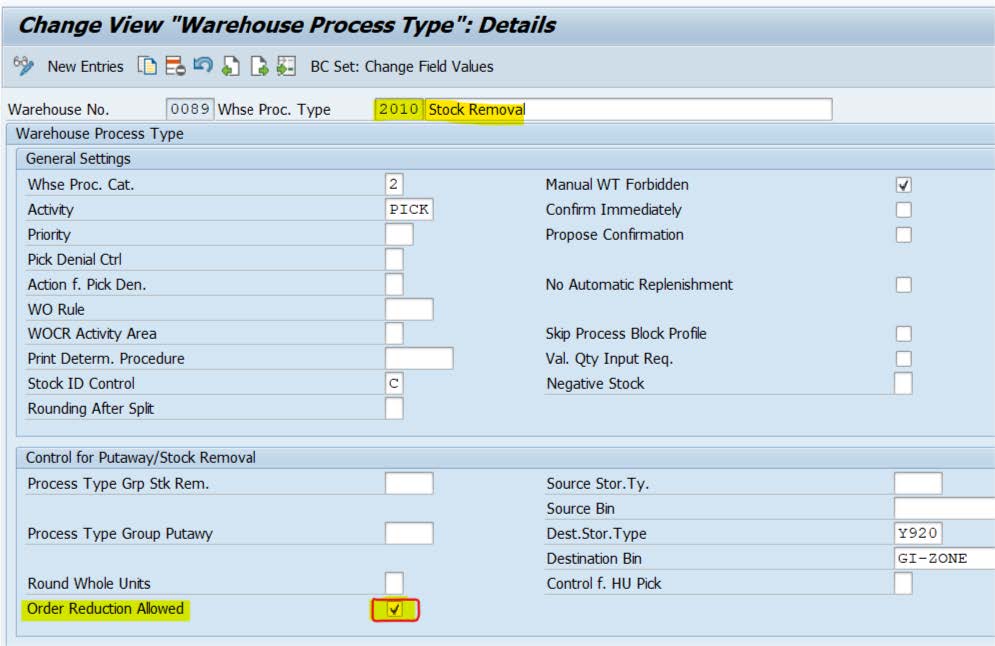
● At Item type(ODLV, PDO) : Activate quantity role Reduce By (CANCEL) and Reduced
Quantity ( OQ_RED), for the quantity offsetting profile used in the item type.
Quantity ( OQ_RED), for the quantity offsetting profile used in the item type.

● Activate Status Profiles(ODLV, PDO): In the item type, activate status type Order Reduction
(DCA)
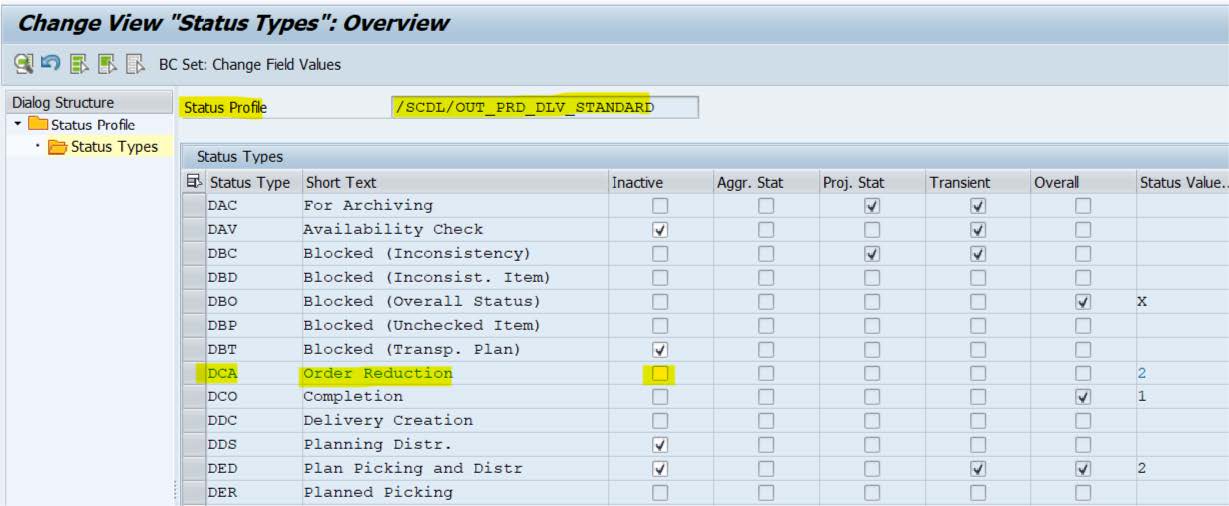
Replication Steps:
1 ) Create a Sales order and Delivery as below
1 ) Create a Sales order and Delivery as below
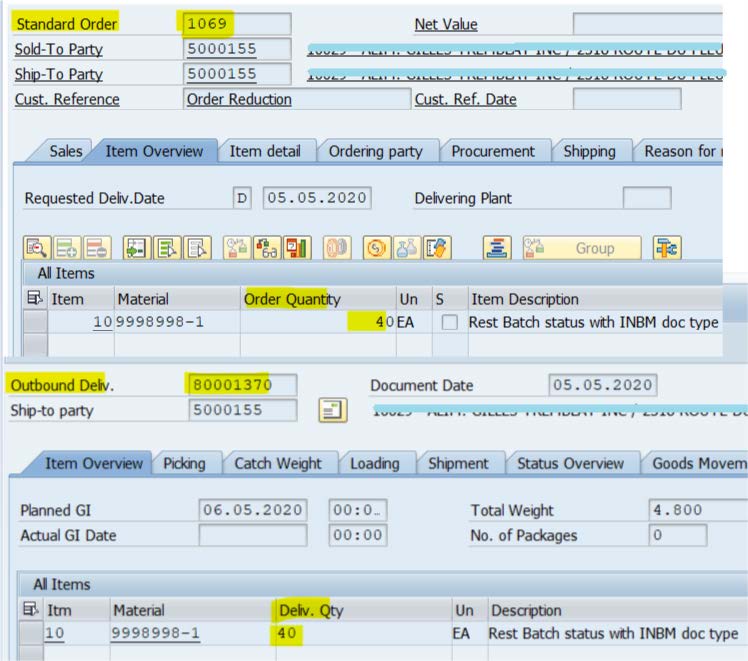
2) The distributed delivery in EWM S4H as Outbound delivery Order(ODO)
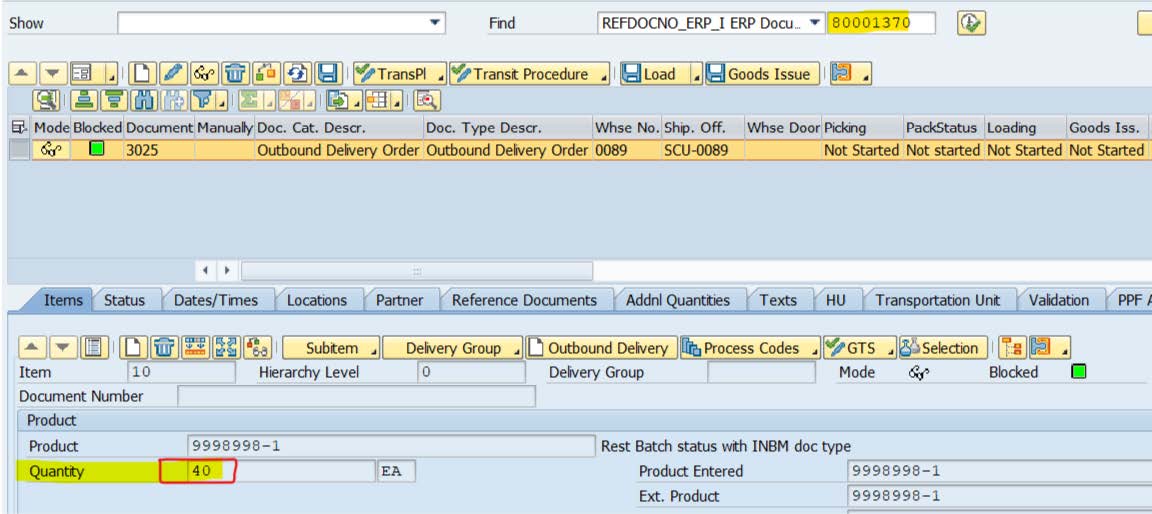
Case-I: When no WT is created.
Change the SO in ERP and check how it impacts the other objects delivery, ODO.
On changing the SO qty 40–>30 EA, the system prompts a message and automatically adjusts the
outbound delivery quantity as well.
Change the SO in ERP and check how it impacts the other objects delivery, ODO.
On changing the SO qty 40–>30 EA, the system prompts a message and automatically adjusts the
outbound delivery quantity as well.
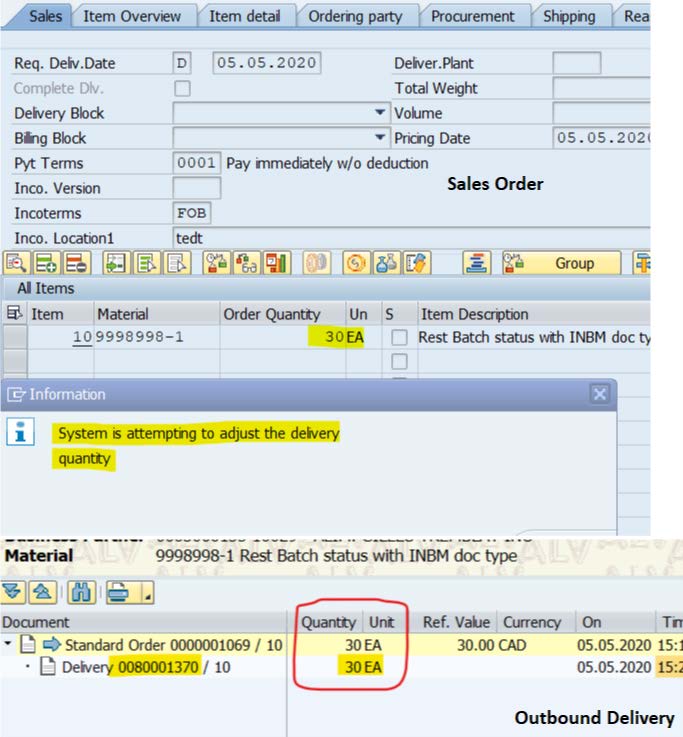
Check the EWM ODO.
The ODO has changed its quantity to 30 pcs.
The ODO has changed its quantity to 30 pcs.
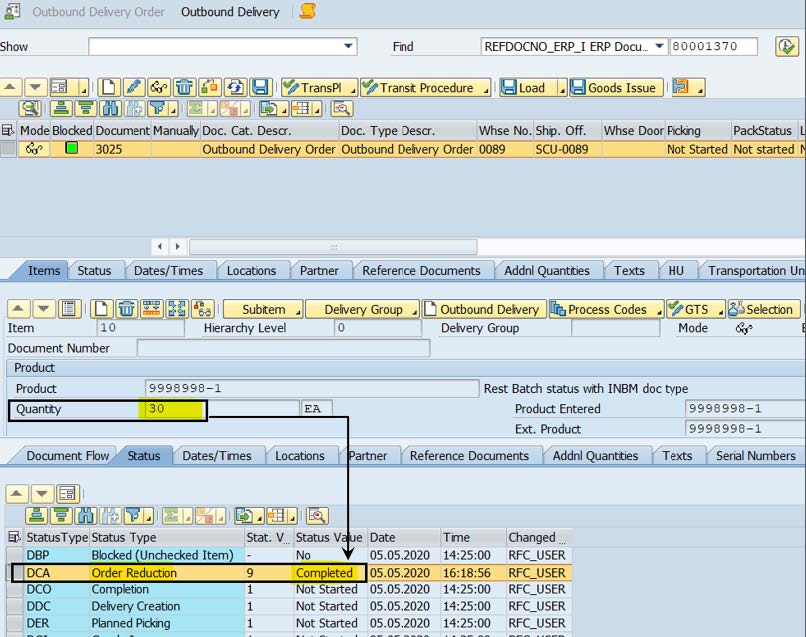
The system has changed the quantity and new status DCA is added.
Case-II: When picking WT is Created but not Confirmed.
● Create a new sales order and new delivery of 12 EA.
● Create a new sales order and new delivery of 12 EA.
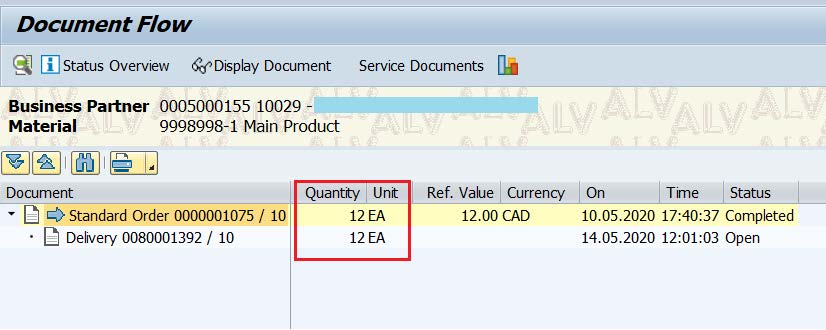
● Check the Picking Warehouse task status in EWM
WT is created but not confirmed.
WT is created but not confirmed.
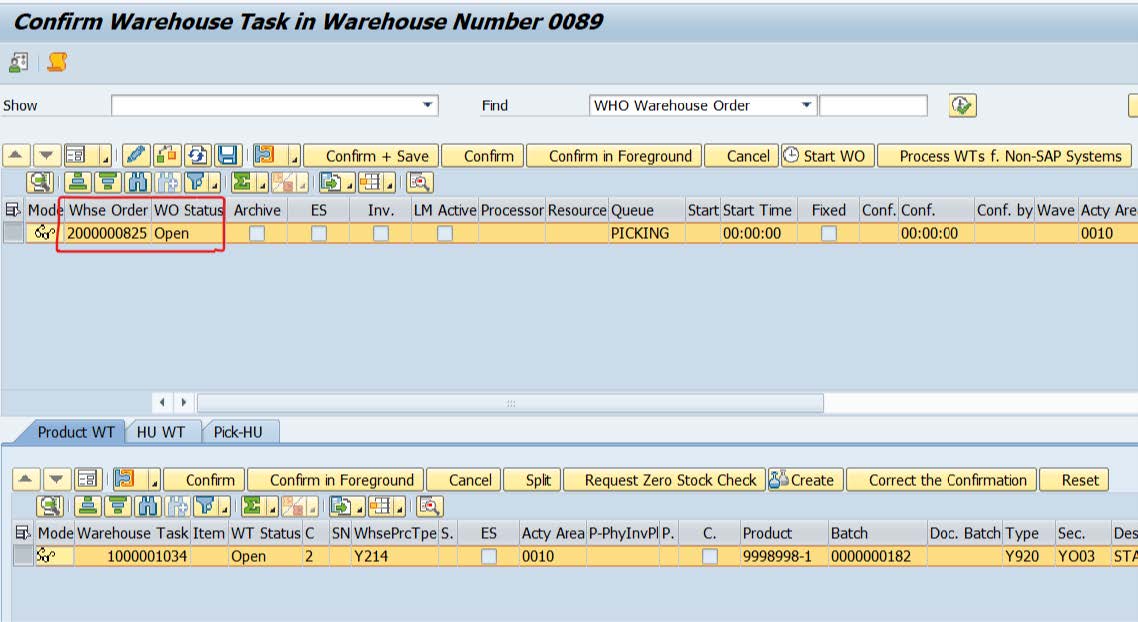
● Change the sales order and see how the noticeables changes in logistics execution delivery and Picking Warehouse Task.
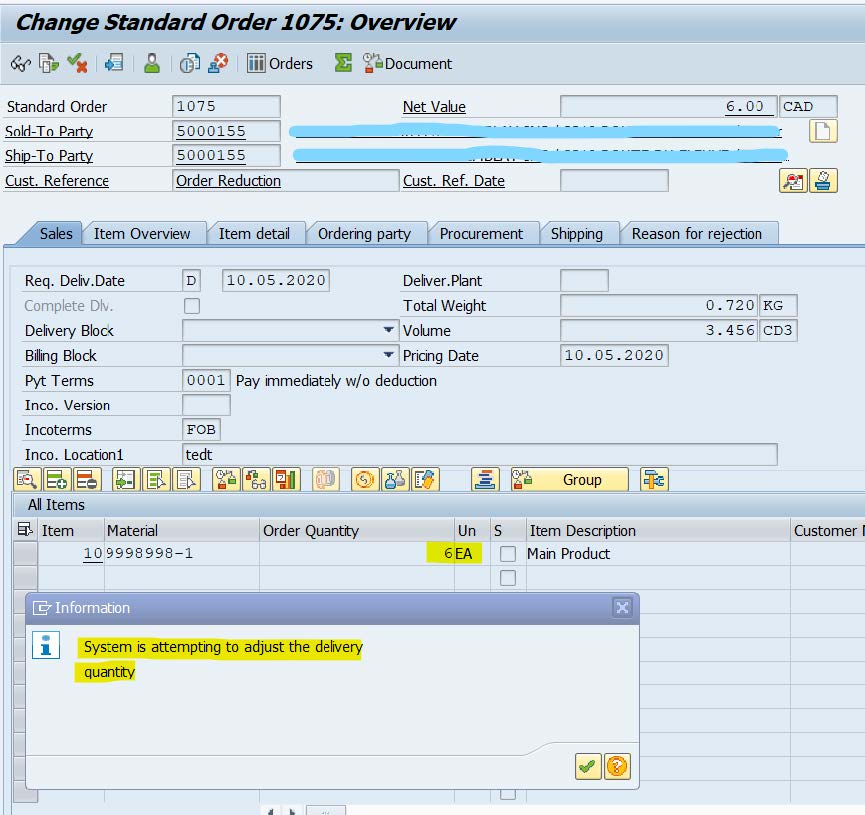
● Check the delivery. The delivery is not adjusted because the warehouse task was created already in EWM.

● Check the EWM Warehouse Task.
Upon a change in Sales order Quantity, EMM automatically cancelled the Picking Warehouse Task.
Upon a change in Sales order Quantity, EMM automatically cancelled the Picking Warehouse Task.
Check the status of WT set by EWM system automatically.
System sets the DCA status and Quantity role through which system reduced the quantity by 6 as Sales order was reduced from 12 EA to 6 EA.
System sets the DCA status and Quantity role through which system reduced the quantity by 6 as Sales order was reduced from 12 EA to 6 EA.
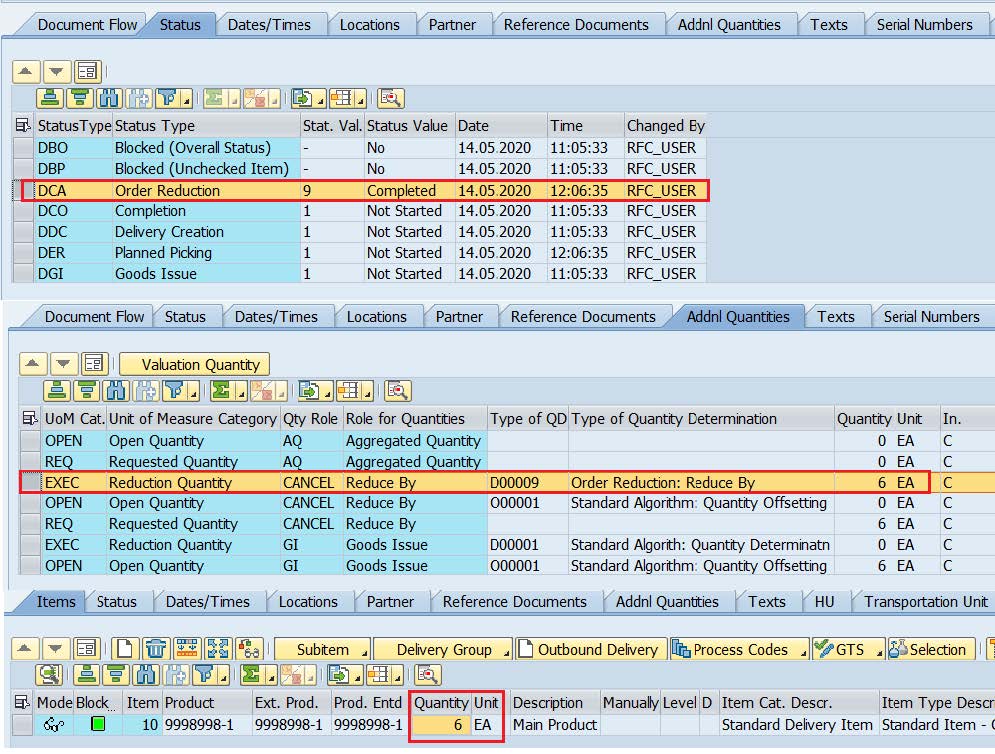
Case-III: When WT is created, Picking and packing is Completed.
Now, when the business is informed that the customer has changed the SO qty from 10 to 5 pcs, the Salesperson changes the SO qty
Now, when the business is informed that the customer has changed the SO qty from 10 to 5 pcs, the Salesperson changes the SO qty

But, the outbound delivery is not adjusted(10 pcs) as Sales order quantity because the Warehouse activity is already completed with Picking and Packing status completed. In this case, since warehouse processing has already started, ERP S4H systems do not receive a final update of the quantity until a goods issue is posted from SAP EWM.
Also the EWM ODO quantity is same as 10 but an extra ‘’Order Reduction’’ confirmation message is sent from ERP to EWM and ODO has status DCA=1( Not started)
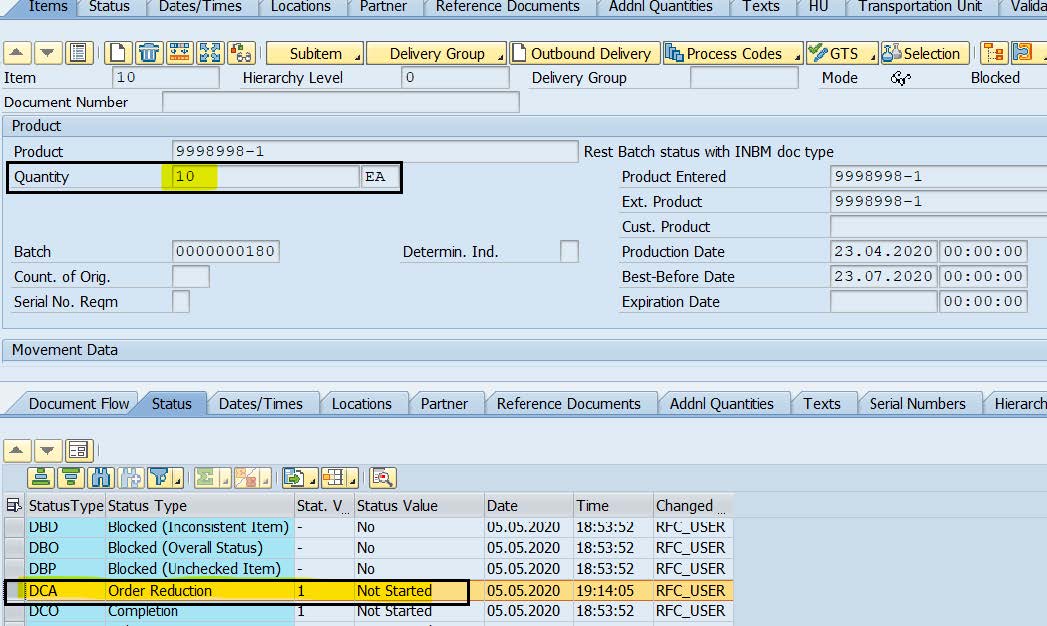
Repacking Products Subject to Order Reduction subject to Case III.
Since the above warehouse task of picking has already been confirmed, stock marked for order reduction can be identified ‘’ by the corresponding checkbox at the work centre.’’
The warehouse worker is informed when packing that SO quantity is reduced. The stock item loses the reference to the outbound delivery order and the quantity of the outbound delivery order item is reduced.
Since the above warehouse task of picking has already been confirmed, stock marked for order reduction can be identified ‘’ by the corresponding checkbox at the work centre.’’
The warehouse worker is informed when packing that SO quantity is reduced. The stock item loses the reference to the outbound delivery order and the quantity of the outbound delivery order item is reduced.
Since the warehouse has the order reduction enabled in configuration, hence during scanning a cancelled product, a message informs the warehouse worker that he/she should exclude this product from the outbound process.
At the repack product tab, the system gives Warehouse workers that picking task is subject to Order reduction.
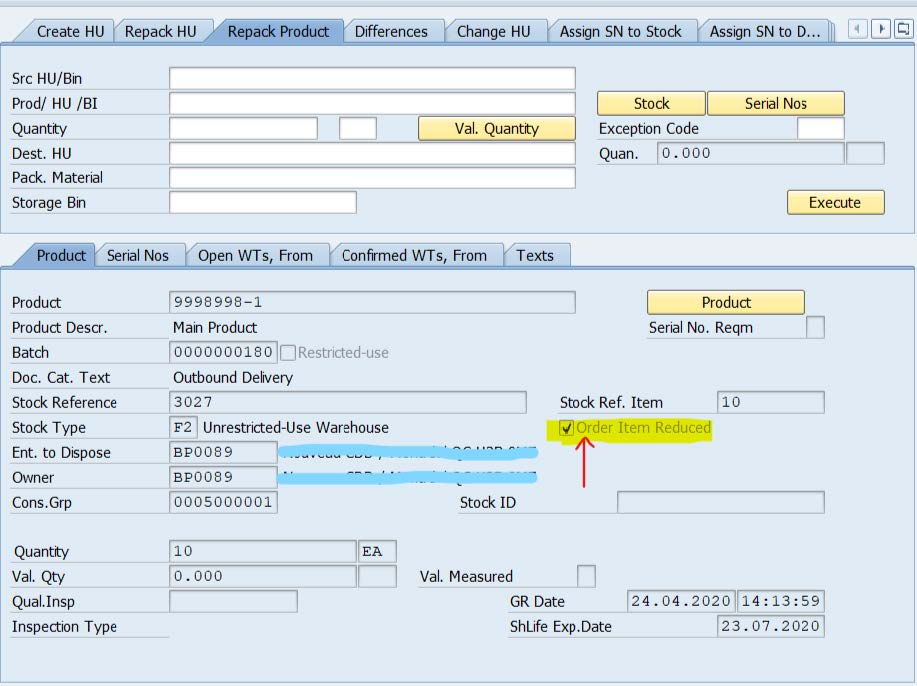
Since, we reduced the sales order from 10 to 5 pcs during packing, Warehouse worker during scanning the cancelled product, he/she can repack the product at “Pick Point’’ and later transfer the HU to the source Bin and ship the remaining quantity to the customer.
● The System generates an alert to the Warehouse picker not to proceed with the picking as the customer has reduced the sales order quantity.
● The System generates an alert to the Warehouse picker not to proceed with the picking as the customer has reduced the sales order quantity.
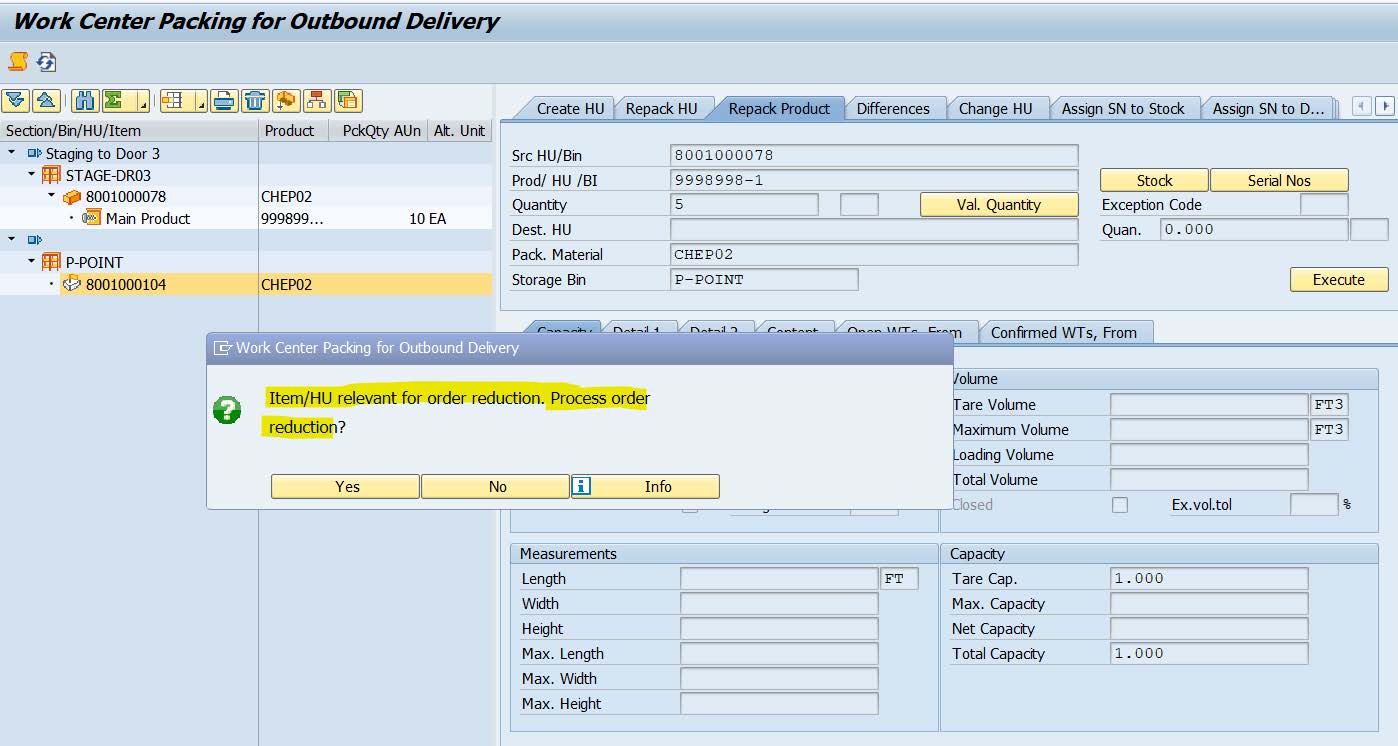
● Warehouse picker gets an active alert and hence no reduced quantity can be shipped to customer.
On selecting ‘’YES’’
System follows the order reduction process. In this case, the shipper does not send the affected items to the customer. the shipper actually repacks the excess stock into an HU that is not connected to any delivery process. Shipper then creates a new HU. As soon it is repacked with the excess stock, the system cancels picking for the affected items so that the stock can be put away again.
System follows the order reduction process. In this case, the shipper does not send the affected items to the customer. the shipper actually repacks the excess stock into an HU that is not connected to any delivery process. Shipper then creates a new HU. As soon it is repacked with the excess stock, the system cancels picking for the affected items so that the stock can be put away again.
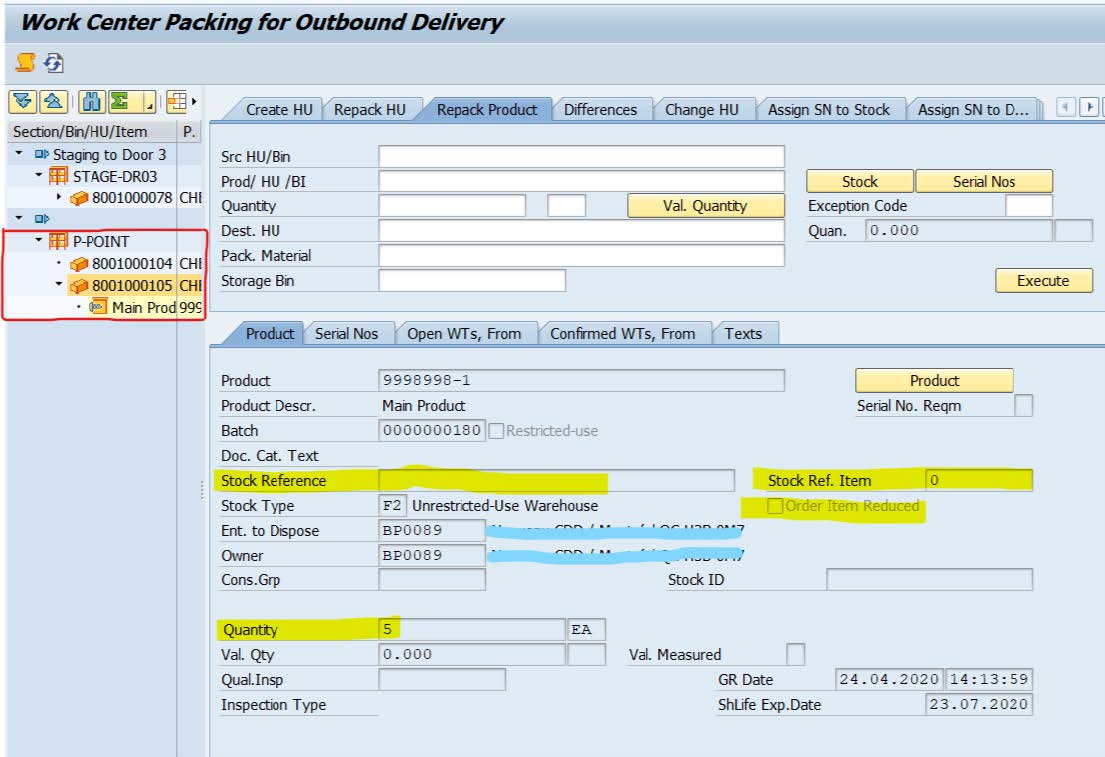
The reduced item loses items to delivery and hence it can be retransferred to the source storage type and remaining quantity can be shipped to the customer.
Stay tuned for more insights on Eursap’s Blog…
Nenhum comentário:
Postar um comentário